5-Minute Tour of an Investment Casting Foundry
Thanks for checking out the IPC Foundry Group! Have you ever wanted to see what happens inside a modern investment casting foundry? If so, it's your lucky day! In today's blog, we'll take a whirlwind tour of our Lindon, Utah facility. Throughout the article, we'll look at some of the automation and equipment that allow for high precision and lightning-fast turnaround times. We'll also answer a few FAQs we get about our foundry, equipment, and the casting process.
Let's get into it!
An outside look at our foundry in Lindon, Utah
Where is the IPC Foundry Group Located?
Our Lindon, Utah facility is one of our two US-based foundries (with the other located 45 minutes outside Austin, Texas). Lindon is 45 minutes south of Salt Lake City, Utah, in the shadow of the Wasatch Mountains, and has been home to the IPC Foundry Group for 44 years (since 1980)! IPC has served thousands of clients across dozens of industries, from aerospace to agriculture and everything in between.
Our Utah facility is positioned to cater to clients throughout the Western United States. Just a stone's throw from the I-15 and minutes to I-80, metal parts can be shipped in Utah and to neighboring states such as Idaho, Wyoming, Nevada, California, Washington, Oregon, and Colorado in a matter of hours. Beyond the West, our facility extends its reach to clients across the US and Canada, promising high-quality castings and an exceptional team to help you with each step of your manufacturing journey.
First Steps Inside the Foundry
We'll breeze through the office environment, but upon arrival, you'll see our reception area, conference rooms, and people at work on investment casting projects. At our Utah facility, we're constantly at work providing rapid prototyping services, 3D modeling, and more. We take great pride in our ability to optimize your production through automation, investments in our equipment & facilities, and our unwavering commitment to being a casting partner you can count on time and time again.
We're a 24/7 production facility. If you ever want to check in on your parts, let us know, and we'll set it up whenever you're available!
Inside the Wax Injection Room
Now, onto some of the good stuff! Our wax injection room features several state-of-the-art injection machines, allowing our staff to print hundreds or thousands of wax molds daily.
We will provide tooling and molds that allow us to make thousands of wax replicas of your metal parts for the investment casting process.
With dies in hand, each of our machines can produce multiple wax copies of your part every 2-5 minutes, significantly reducing turnaround times for the casting process. After molds are finished, staff will provide QC and cluster wax parts into "trees." These trees allow our foundry workers to cast multiple metal parts in one pour. During our onboarding process, we'll work with you to optimize your part to our process and equipment so you can get the highest quality parts in the quickest time possible; trees are just one component of this optimization.
These machines also allow for rapid prototyping and first articles. Our engineering team can work with you to iterate several versions of your metal part in the pre-production stage, and the wax injection allows for high-quality, to-scale models in a matter of minutes. We can expedite the production of these wax models and send functional metal prototypes in just a few days.






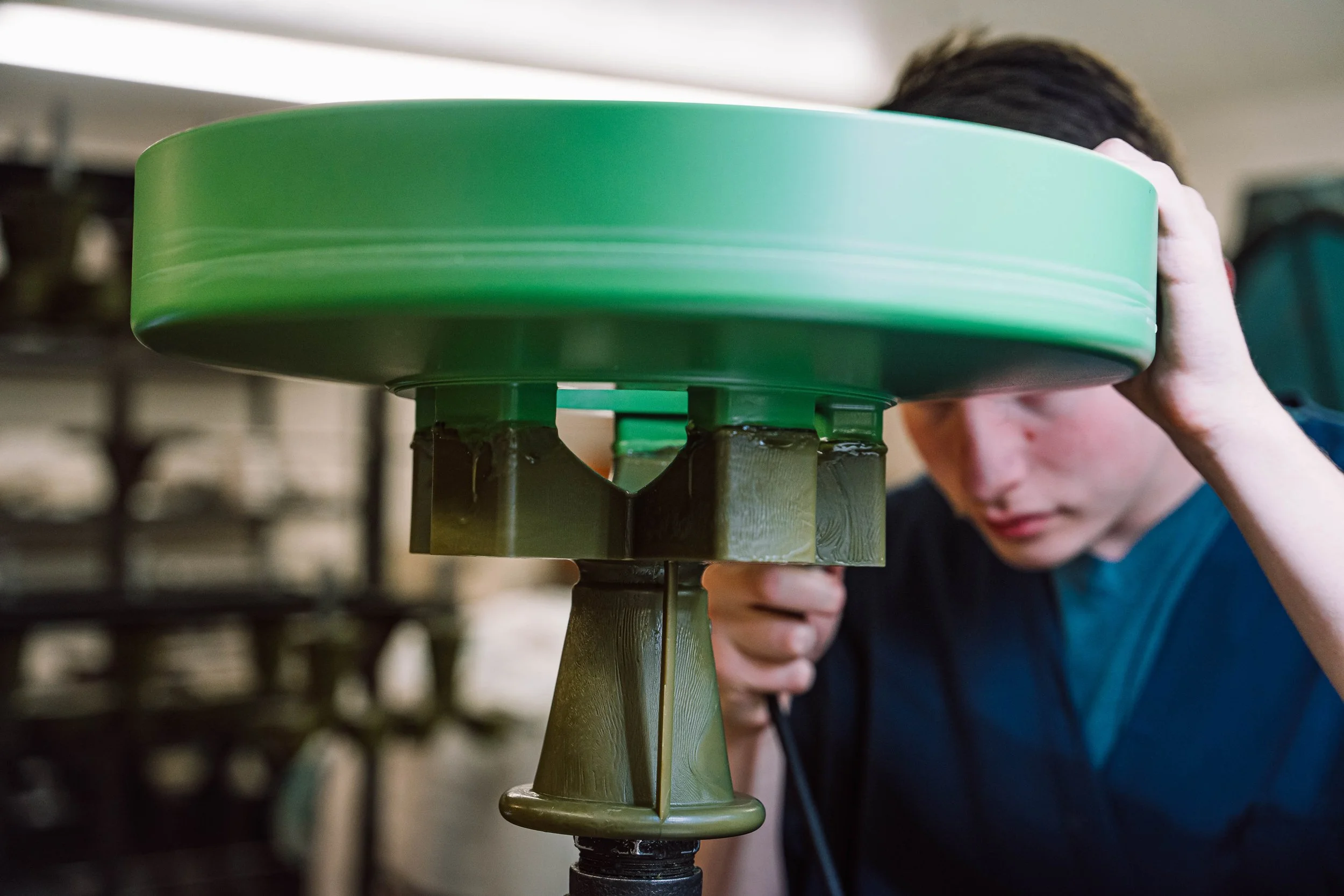

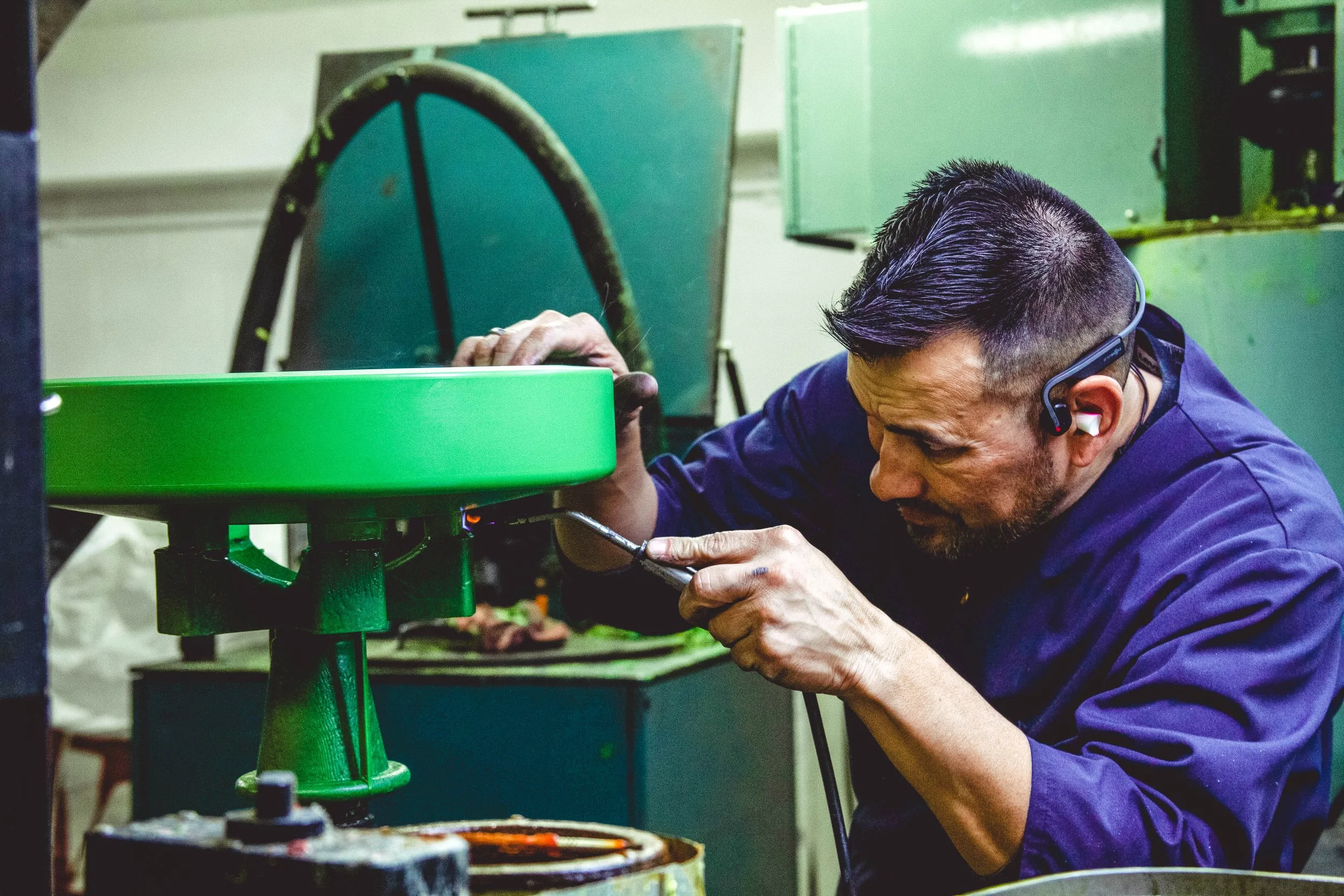
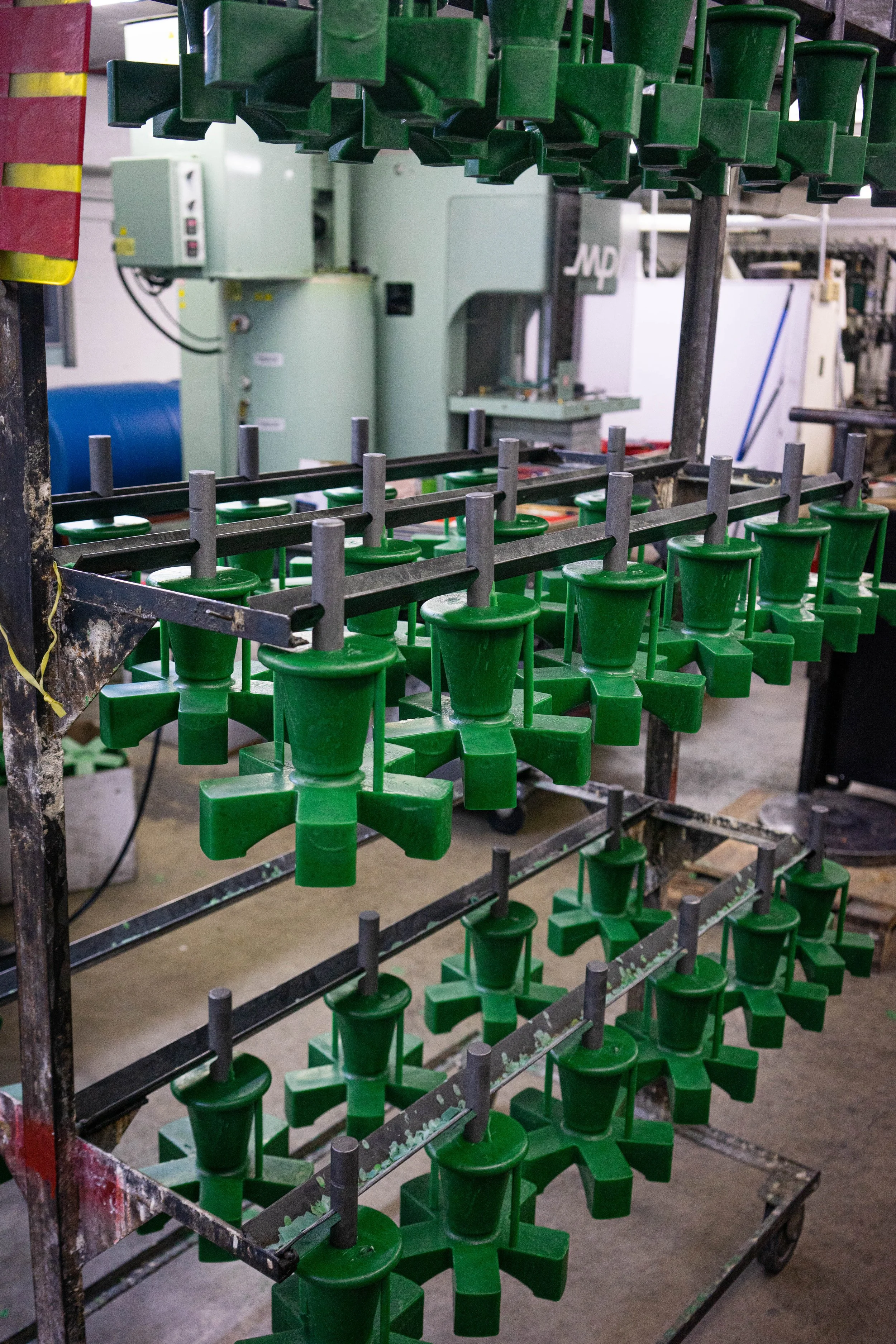

FAQs on Wax Injection
-
Our wax injection machines can print a single large part or dozens of smaller parts every 2-5 minutes. With multiple injectors in our arsenal, we produce thousands of molds daily!
-
It depends on the size of your part! To optimize production, we spend time developing gates and trees before production begins. In short, we put as many parts in a tree as possible without sacrificing quality; this can mean just one large casting or dozens of smaller casts.
-
Typically, we hang onto tooling for future production runs. That being said, once your production cycle is completed we’re happy to send you the tooling to keep internally.
Ceramic Slurry, Rainfall Sanding, and Robotics
Moving forward through the facility, we enter the slurry room. Here, wax models from the previous step are coated in a ceramic slurry that will serve as the mold for your metal parts.
We've implemented custom robotics that allows for incredible precision and around-the-clock production. The robots will dunk the wax molds in a slurry tank, insert them into the rainfall sander, and then mount them onto our specialized conveyor track.
These robotics allow us to be more precise than ever, creating narrower tolerance windows, less human error, and the capability to form even more complex castings. Our Utah facility alone produces more than 15x the metal parts than we were just five years ago.
A robot dipping two wax patterns into ceramic slurry
After dipping, wax patterns are also held under our rainfall sander, where additional components of the shell are added to the mixture.
Wax parts in the early stages of the ceramic slurry process. You can see the precision that investment casting affords with the noticeable text on the part.
Another shot of our robotics and rainfall sander.
A wide angle shot of our Utah foundry’s slurry room
Our robotics placing freshly dipped and sanded ceramic shells onto our conveyor system. These robotics have enabled us to produce metal parts around-the-clock.
Ceramic Slurry FAQs
-
This depends on the size of the part! Our engineering team works hand-in-hand with the production team to get your parts through this part quickly while still providing the highest quality results.
-
The slurry is made up of a binding liquid combined with small ceramic pieces (typically silica, alumina, or similar).
Our Utah Foundry's Conveyor System
Our one-of-a-kind conveyor system works hand in hand with our robotics to provide a seamless 24/7 production window. During the investment casting process, wax molds must be dipped in slurry multiple times to create a shell strong enough to hold molten metal. Between these dips, the slurried parts need time to dry. What once was a labor-intensive process has been streamlined to perfectly timed dips and an optimized cycle.
Our robotics have been programmed to add and remove slurried parts to the conveyor system like clockwork, allowing us to engage in each step of the investment casting process without delay: no idle time and a proper 24/7 production cycle for your metal parts.
Our conveyor system allows for simultaneous drying, dipping, and rainfall sanding during our production cycle.
Looking down on the robotics, slurry tanks, rainfall sanders, and conveyor system working in tandem at the IPC Foundry Group’s Utah Location.
Ovens and Foundry
Just beyond the slurry room sits our foundry. Ceramic shells from the previous steps have been hollowed out via flashfire autoclave and are superheated in preparation for pouring your selected alloys.
It can get quite loud here, but watching molten metal turn your part from concept to reality is fascinating. After pouring, the parts will cool and move on to finishing work.
A foundry worker inspecting a crucible before metal pouring.
A hollow shell being filled with molten metal in our foundry room.
A foundry worker pulling a pre-heated shell out of one of our superheating ovens.
A quick GIF of metal pouring at our Utah facility.
Metal Finishing Work
At IPC, we offer numerous finishing options, including sanding, stamping, painting, machining, testing, and heat treating. In a future blog, we'll explore each of these in greater detail as they go beyond the scope of our quick tour.
At IPC Foundry Group, we've worked hard to provide a one-stop shop for all your investment casting needs. If you have a specific challenge or need for your next metalworking project, don't hesitate to contact our team to help you make it happen.
Grinding off gates or sanding imperfections is just one aspect of finishing work done at IPC Utah.
Wrapping Up
Thanks for joining us for this whirlwind look at the IPC Foundry Group's Utah location! We offer FREE in-person tours at each of our facilities. If you'd like to book a tour, you can do so by clicking here!
If you'd like to learn more about the investment casting process, check out our breakdown of each step here.